Pipe inspection robot WATER Series
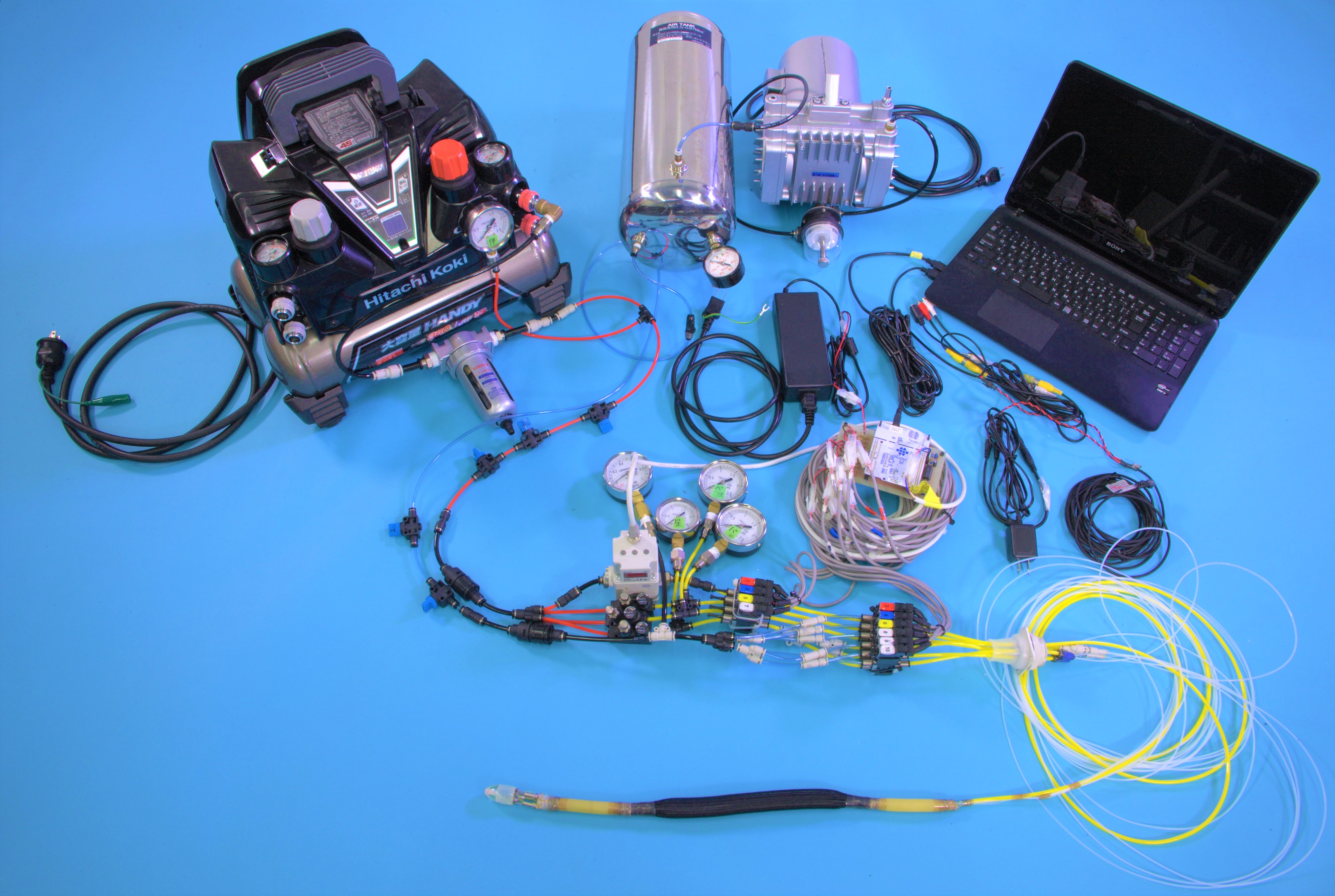
Pipe inspection Robot
Overview
"WATER (WasedA Tokyogas Endoscope Robot) ", is a robot developed to locomote and detect inner environment in gas pipes.
It can locomote forward and backward like an inchworm according to the following phase and change locomotion directions.
The robot consists of a Thrust Force Generation Module and an Active Bending Module which are driven pneumatically. With the modules and a camera,
the robot is capable to locomote in the horizontal and vertical pipes with inner diameters of 28[mm] and 53[mm] and enter and withdraw from pipelines with 8 curved pipes (2 elbows, 4 bends, 2 Tees).
In addition to the above functions,
we developed WATER-5 in 2019 to enter and withdraw from overturning and lateral swing with inner diameters of 53 [mm];
WATER-6 in 2020 to locomote at a length of 50 [m] in a main branch pipe inner diameters of 53 [mm],
and WATER-7 in 2021 to insert and withdraw into a meter gas cock.
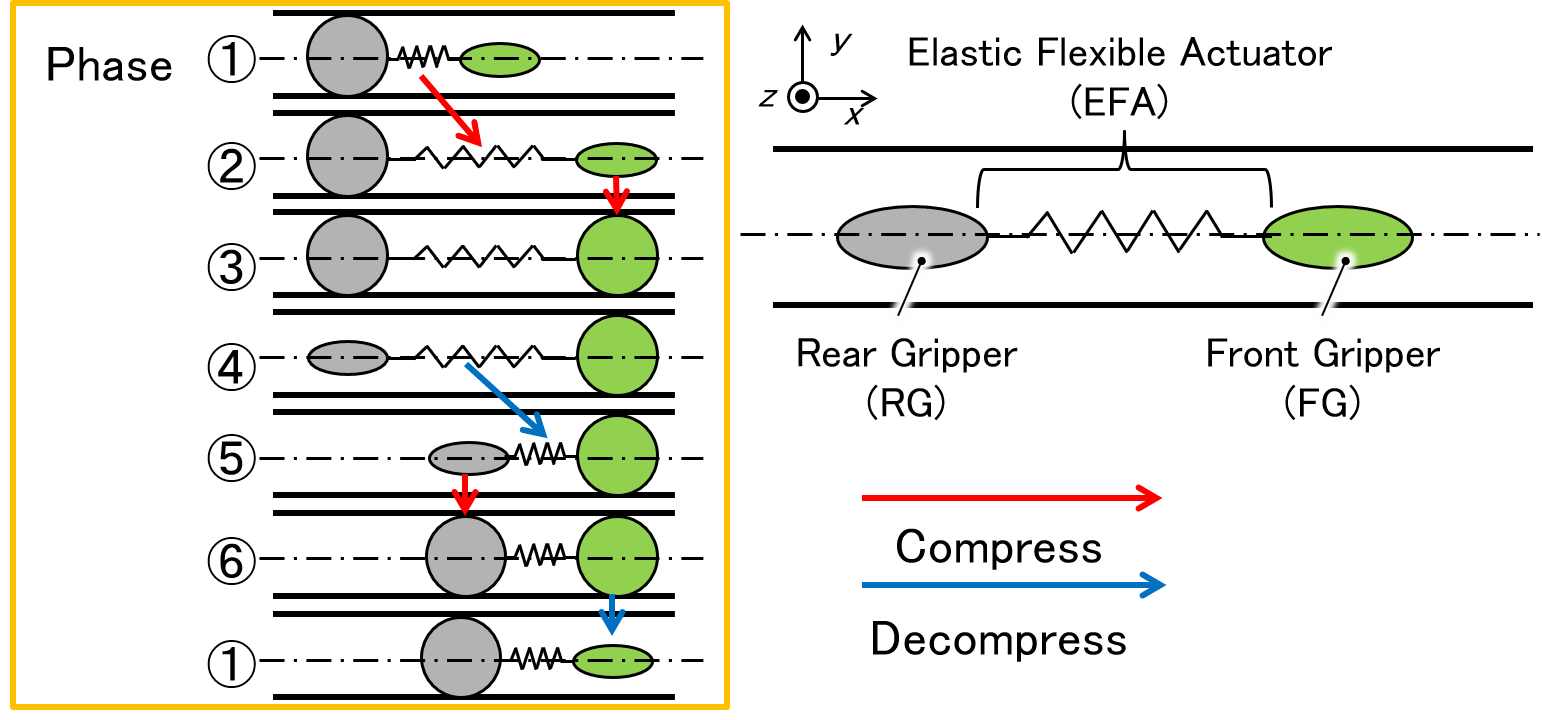
System
Cables of the camera and air supply tubes of modules are connected to the machines on the ground as shown in the following picture. There are pneumatic devices to drive each module of the robot and a PC for operation, so that the robot can be operated manually while viewing the images from the camera.

Research Contents
WATER-7 (2021)
The previous robots were not suitable for insertion from meter gas cock with small hole widths. With the goal of installation on-site, the robot is required to be inserted from meter gas cock within 30[min], retrieved within 15[min], and repeatedly used without major damage 30 times. Therefore, in this study, we improved the robot into a new type, WATER-7, which is able to be inserted and removed from meter gas cock, travel a service pipe shown in the picture below in a short time, and has high durability and robustness.
The improvements of WATER-7 compared with the previous robots can be given below as five points.
Miniaturization of each part of the robot
2.Development of Active Bending Module (ABM) that maintains the previous bending angle
3.Development of Thrust Force Generation Module with a smaller diameter and higher durability
4.Modification in the incorporation method of air supply tubes for Front Gripper(FG)
5.Improvement in methods of sealing and connections between components
As a result, WATER-7 is confirmed to insert from meter gas cock, travel a service pipe made of steel within 81[min], and be used repeatedly up to 9 times.
However, since it has not reached the achievement for on-site installation, the robot still needs further development.
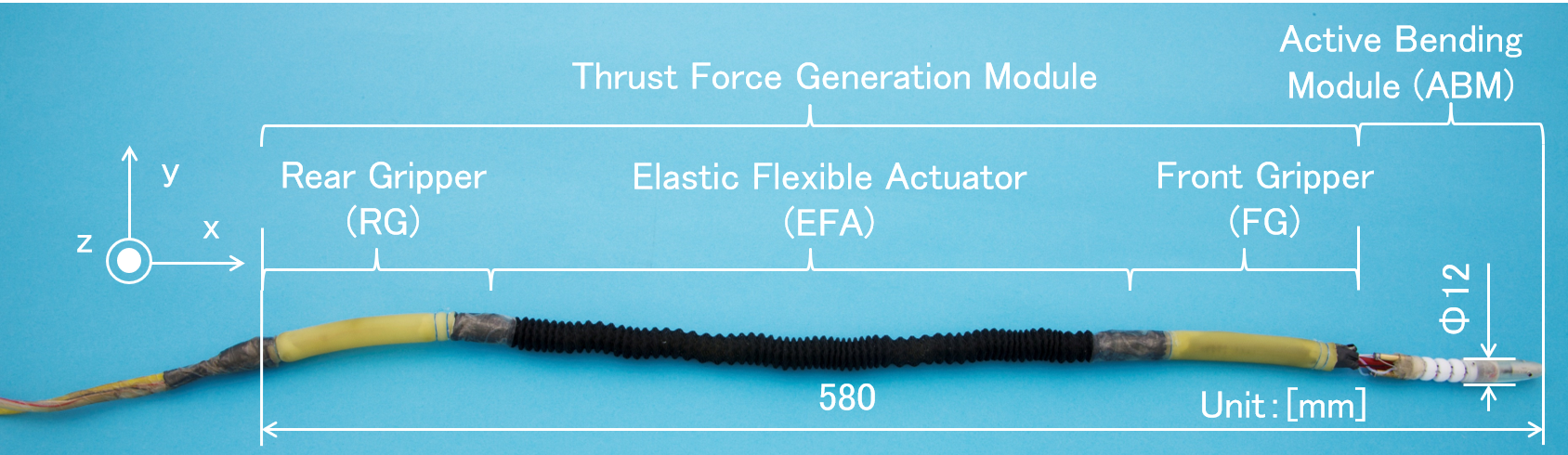
WATER-7

Target environment
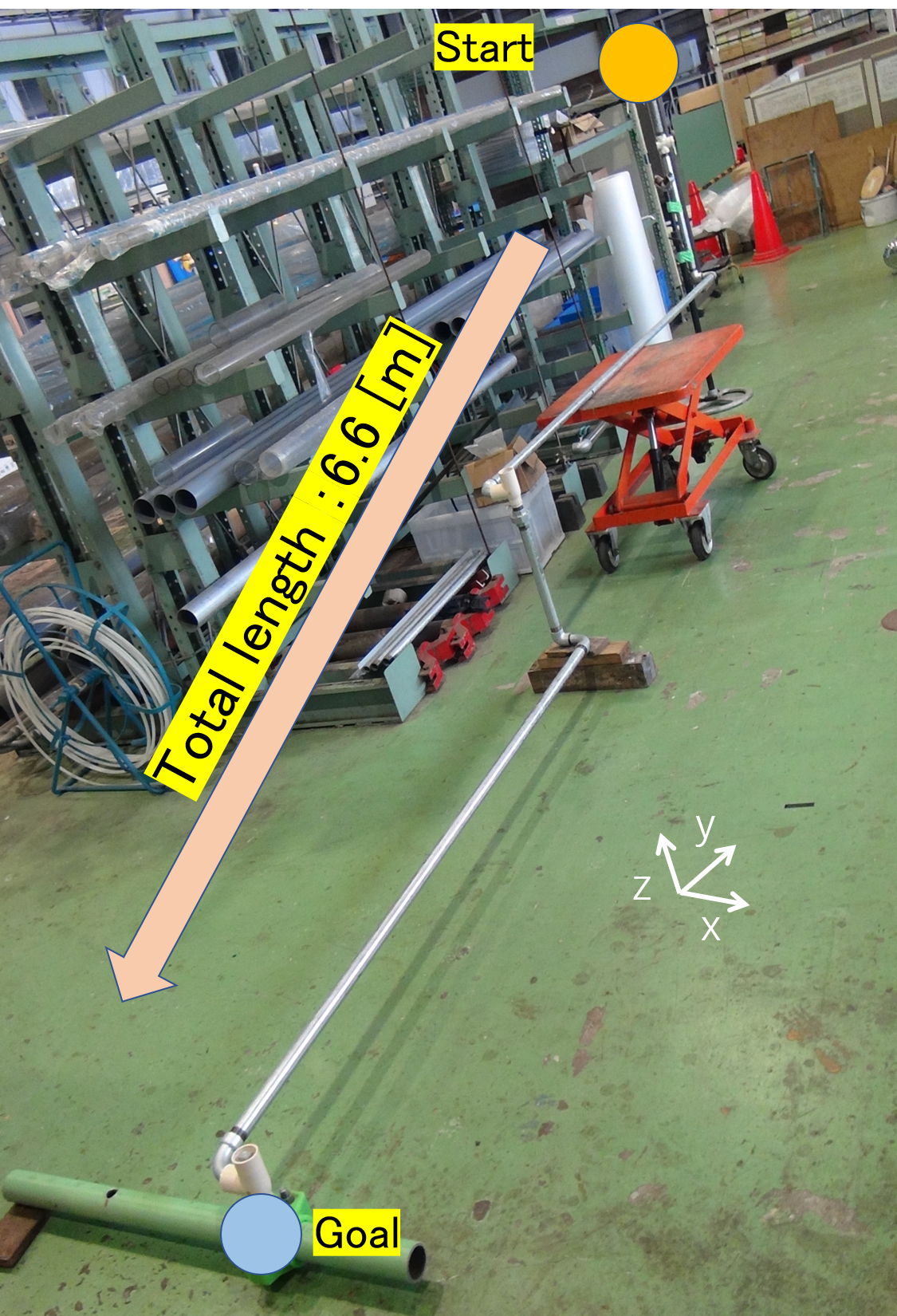
Picture of experimental piping at Tokyo Gas
[関連論文]
磯野琉,沈陽,児玉理,小西瑶果,井上大雅,大貫彰彦,前田亮,石井裕之,高西淳夫,”メーターガス栓および灯外内管・供給管への挿通・撤収が可能な空気圧駆動型ガス管内移動ロボットの開発 第1報:ロボット外径の小径化および挿通時間の短縮”,第40回日本ロボット学会学術講演会,
3G1-01, 東京都, 2022年9月
沈陽,磯野琉,児玉理,小西瑶果,井上大雅,大貫彰彦,前田亮,石井裕之,高西淳夫,”メーターガス栓および灯外内管・供給管への挿通・撤収が可能な空気圧駆動型ガス管内移動ロボットの開発 第2報:高耐久な推進モジュールの開発およびロボット堅牢性の向上,第40回日本ロボット学会学術講演会,
3G1-02, 東京都, 2022年9月
WATER-6 (2020)
Although WATER-5 can pass through all the bends in the assumed pipe, it could not travel in the deep part of the gas pipe. Therefore, we developed WATER-6, a robot that can travel at a depth of 50[m] in a gas pipe, assuming an actual inspection in a gas pipe. WATER-6 is equipped with an elastic flexible actuator with a reverse winding mesh spring that combines a right-handed spring and a left-handed spring. WATER-6 can locomote in a steel pipe while exerting a traction force of 76 [N]. The robot was made to run through a 50 [m] pipe with eight bends that mimicked a real gas pipe, and it was confirmed that the robot could run at a depth of 50 [m] in the gas pipe.
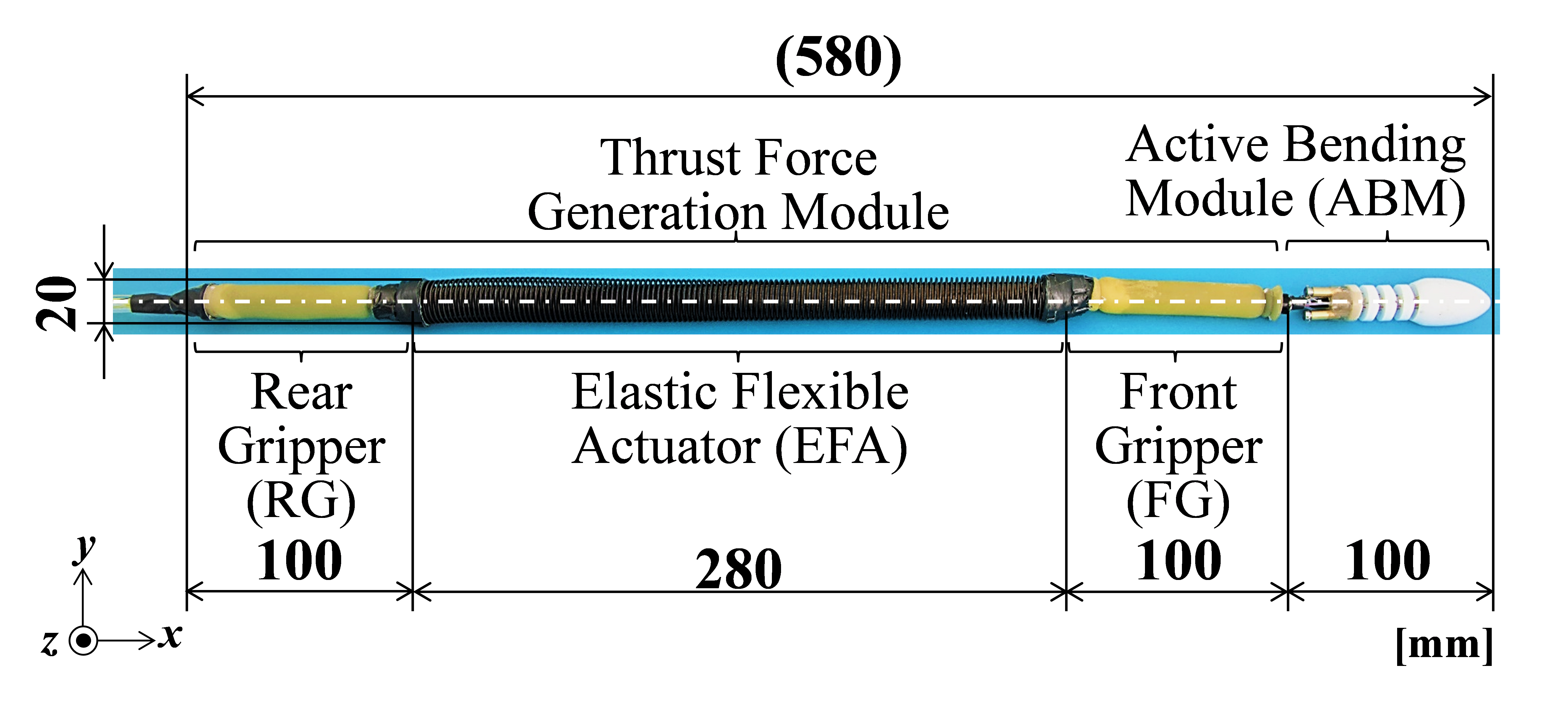
ガス配管深部50 [m]地点で約80 [m]の送気チューブを牽引しながら走行するWATER-6 (16倍速)
[関連論文]
小西瑶果,先﨑翔太郎,中村蒼子,児玉理,清水智壮,大貫彰彦,前田亮,石井裕之,高西淳夫
”ガス管本支管深部での走行が可能な空気圧駆動型管内移動ロボットの開発”,第39回日本ロボット学会学術講演会, 2j3-02,オンライン,2021年9月
Satoshi Kodama,Yoka Konishi,Koki Shindo,Shotaro Senzaki,Toko Nakamura,Akihiko Ohnuki,Minoru
Konno,Hiroyuki Isii,Atsuo Takanishi, "Development of Pneumatic Driven Robot System which can Entry and
Retire from Gas Pipe," 2021 IEEE International Conference on Mechatronics and Automation (ICMA), 2021, pp.
1466-1471, doi: 10.1109/ICMA52036.2021.9512655.
WATER-5 (2019)
The WATER-4 had a problem that it took a long time to remove the robot from the main branch and the success rate was low. The WATER-5 is a robot based on the WATER-4, which enables not only the entry of each bend to the main branch, but also the removal of the robot after entry. The newly developed inferior drive type active bending module enables the robot to withdraw from the main branch pipe. The bending angle of the robot is 84[deg], which is higher than that of the conventional robot, and it is easier to enter the curved part.
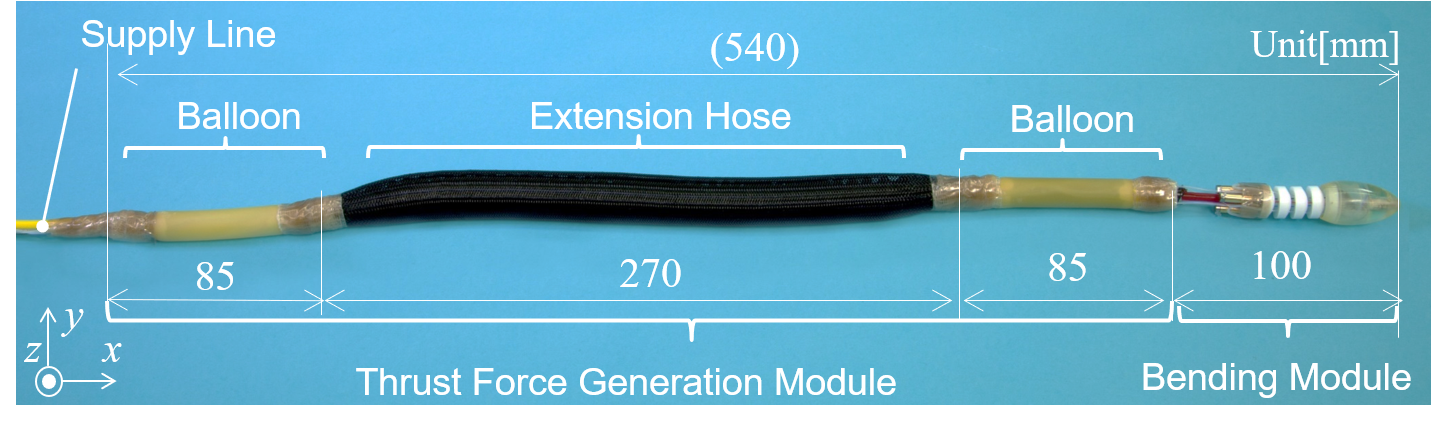
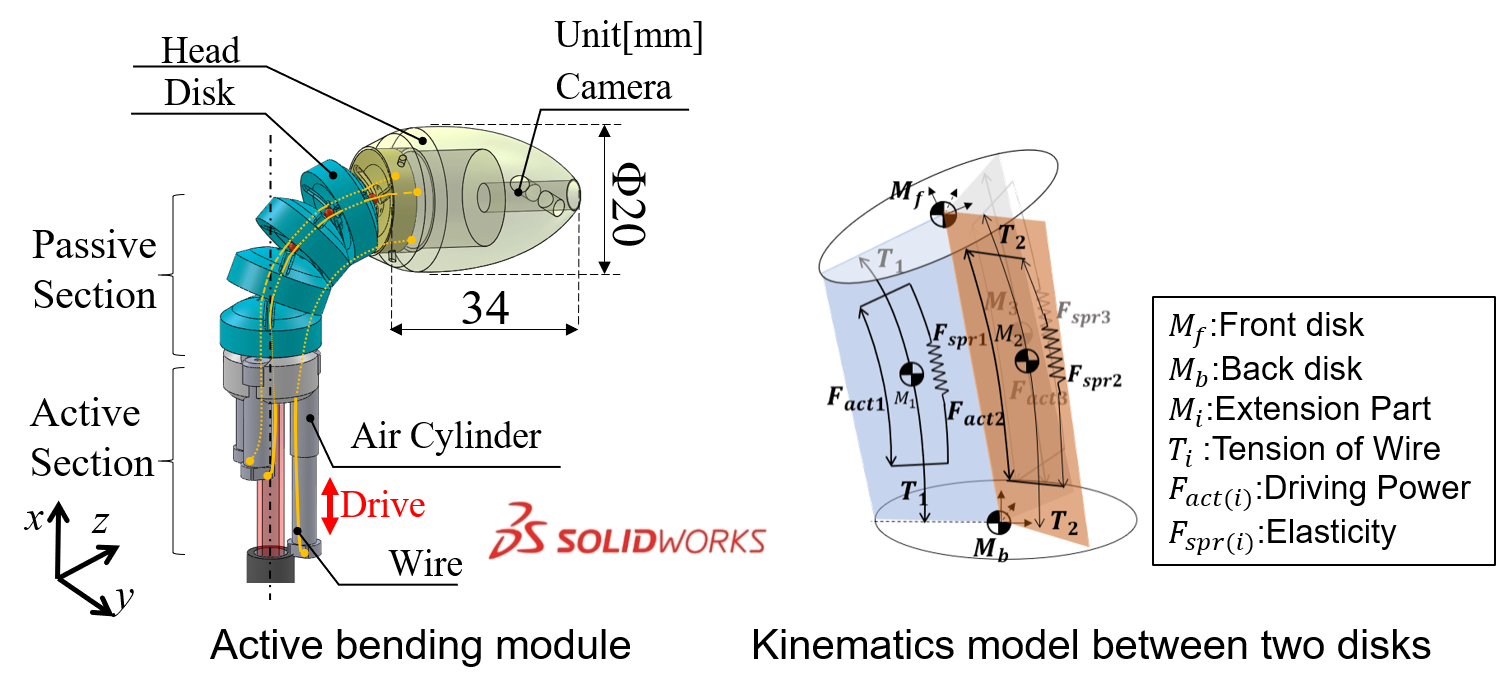
[Research paper (in Japanese)]
児玉理,先﨑翔太郎,中村蒼子,真藤幸暉,今野実,大貫彰彦,高西淳夫,石井裕之,
ガス管本支管への進入および撤収が可能な空気圧駆動型管内移動ロボットの開発,”第38回日本ロボット学会学術講演会”, 3A1-01,オンライン,2020年10月
WATER-4 (2018)
With WATER-3, it was not possible to run the main branch pipe including different diameter cheese, overturning and lateral swing. Therefore, we developed the WATER-4 robot, which is capable of entering the main pipe and passing through the curved part, aiming to enter and remove cheese with different diameters, 50A overturning, and horizontal swing. A cable shorter than the extension hose of WATER-3 was built into the extension hose to enable extension in a curved state, thereby reducing the frictional force on the pipe wall at the curved part and solving these problems.
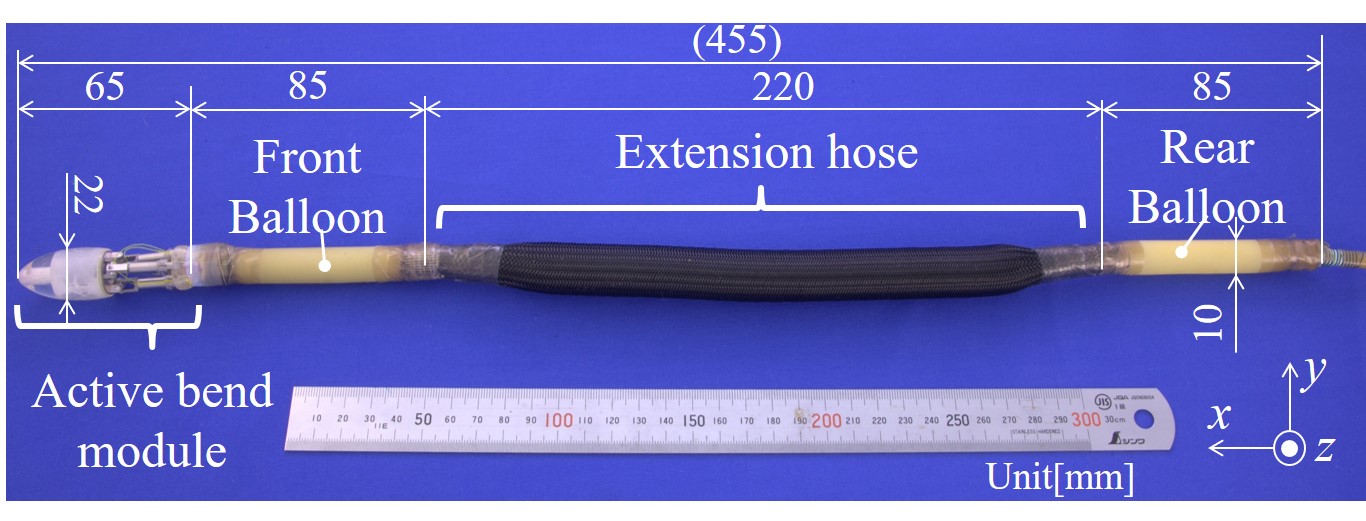
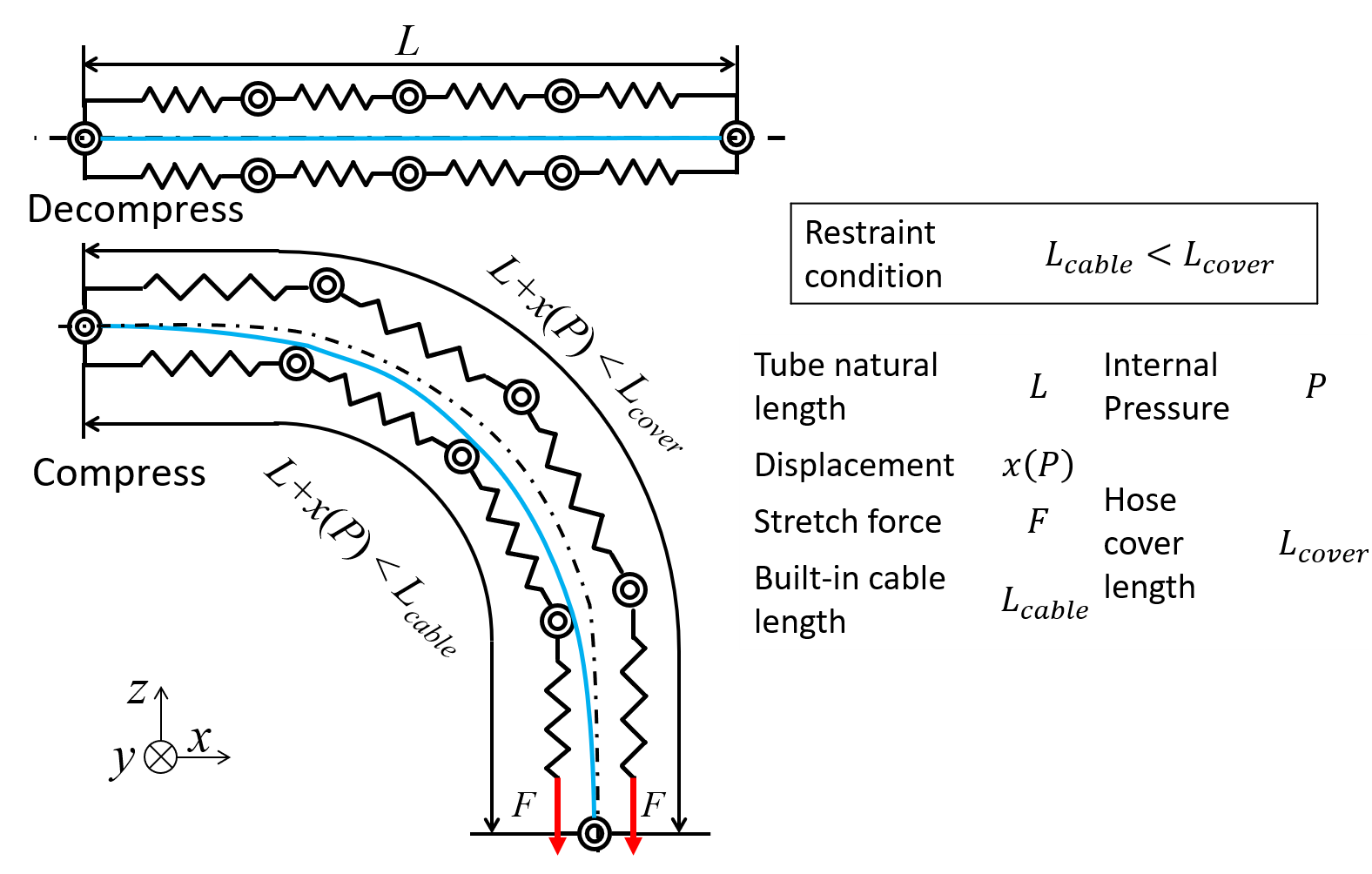
[Research paper (in
Japanese)]
先﨑翔太郎,中村蒼子,真藤幸暉,吉本昂平,今野実,大貫彰彦,高西淳夫,石井裕之,50A管湾曲部への進入および撤収が可能な管内移動ロボットの設計・製作,”第37回日本ロボット学会学術講演会”,
1I2-05, 東京都, 2019年9月
WATER-3 (2017)
Although WATER-2 was able to pass through a simulated 8-bend pipe composed of transparent tubes, the speed
of the robot was too slow for the target work time. Therefore, WATER-3 was developed with the goal of
reducing the passage time of the simulated transparent 8-bend tube to 10[min].
By using natural rubber
tubing as the balloon material, which has high thickness and contraction force, the propulsion cycle was
reduced by about 14%. In addition, it was necessary to slow down the traveling speed at the time of entry,
because the balloon would be damaged if it collided with the vertical part of the T-junction when
traveling under high pressure. By fabricating a metal bending module by cutting, the robot is no longer
damaged and can enter the T-junction pipe without slowing down.
By using the developed robot together with the newly developed tube extruder, the average transit time
was 16 minutes, and the fastest was 10 minutes.
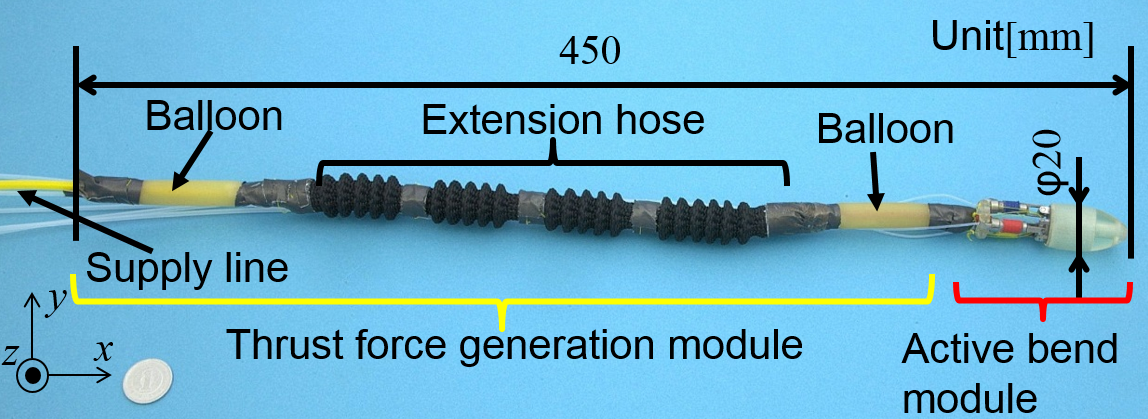
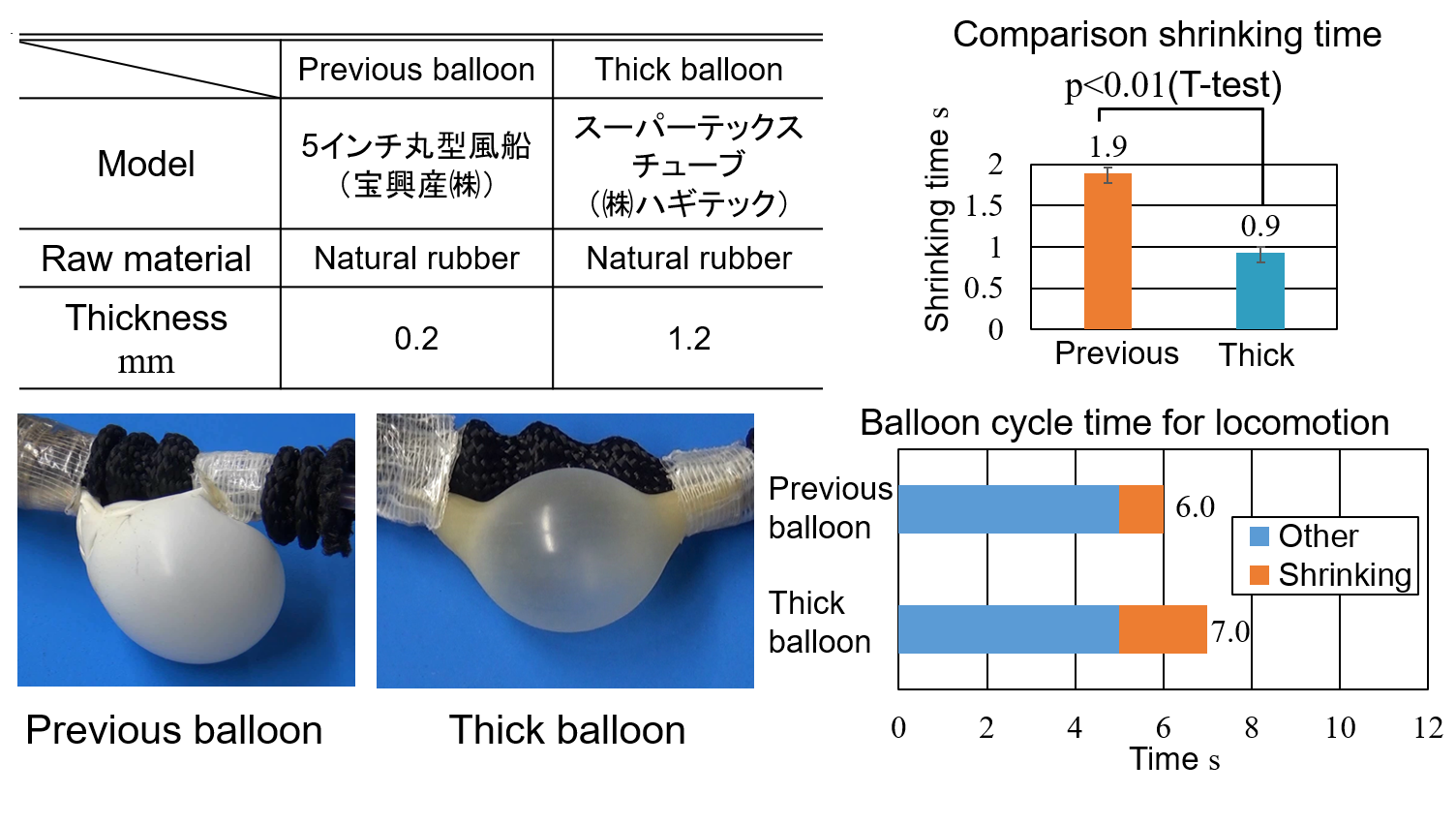
[Research paper (in
Japanese)]
真藤幸暉,吉本昂平,野村幸暉,李駿騁,今野実,大貫彰彦,高西淳夫,石井裕之,高速で湾曲部通過が可能な空気圧駆動型管内移動ロボットの設計・製作,”第36回日本ロボット学会学術講演会”,
3F1-07,2018年9月
WATER-2 (2016)
WATER-1 was unable to pass through the curved part of the 25A pipe. We attempted to solve these problems. To solve the lack of propulsive force, we took the approach of increasing the working pressure of the elongation hose to 0.7 [MPa]. We changed the material of the elongation hose from silicone rubber to natural rubber tube, and confirmed that the elongation hose has low deformation and improved contraction force. We also changed the cover of the elongation hose from a conventional sprinkler hose cover to a bellows folded cover with a different mesh to reduce twisting during elongation. This makes it possible to efficiently convert air pressure into propulsive force.

[Research paper (in Japanese)]
吉本昂平,李駿騁 ,竹内弘美,野村幸暉,今野実,鳥海良一,石井裕之,高西淳夫,” 第35回日本ロボット学会学術講演会”, 2E2-03
,2017年9月
WATER-1 (2015)
We chose the method of propulsion and retraction like a scale insect as the method of traveling in the gas pipe. The designed and fabricated WATER-1 consists of a propulsion module and a bending module. The propulsion module consists of a front balloon, a rear balloon, and an extension hose, and all of these actuators are pneumatically driven. All of these actuators are pneumatically driven. The size of the balloon can be changed according to the amount of air flowing into the balloon, and it can grasp a pipe wall of any size. The elongated hose has the property of extending in the axial direction when pressurized. These actuators are propelled by cyclic pressurization and depressurization. The bending module consists of a three-degree-of-freedom parallel link mechanism, which can bend in any direction by controlling the pressure of three pneumatic cylinders, enabling the selection of branches in the pipe.
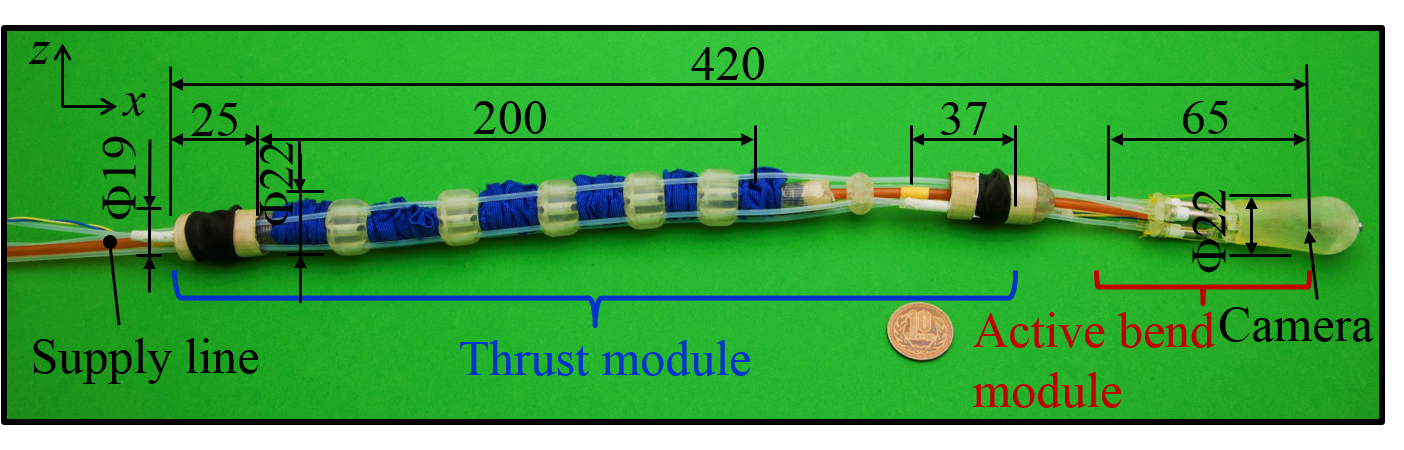
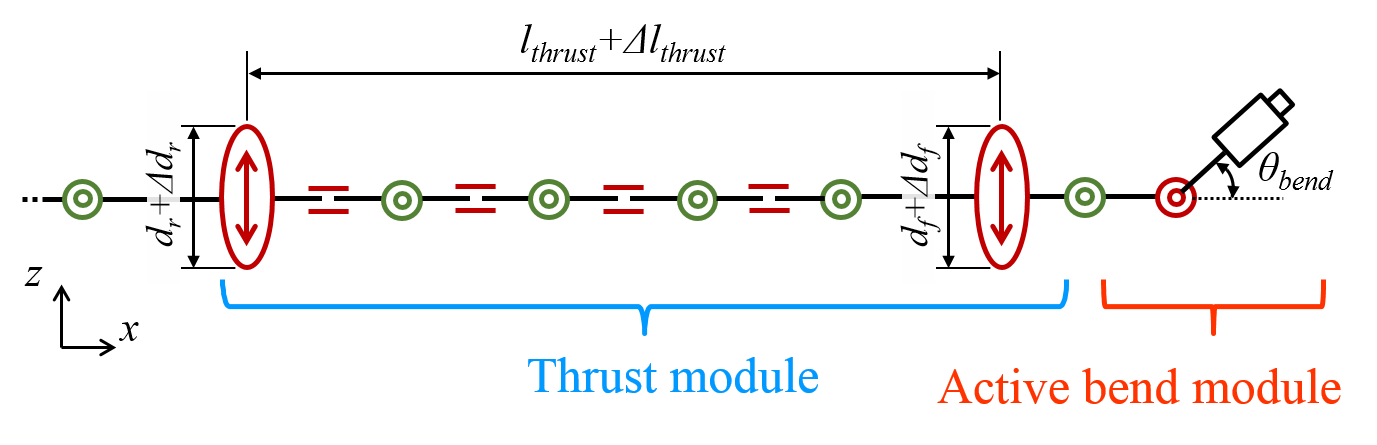
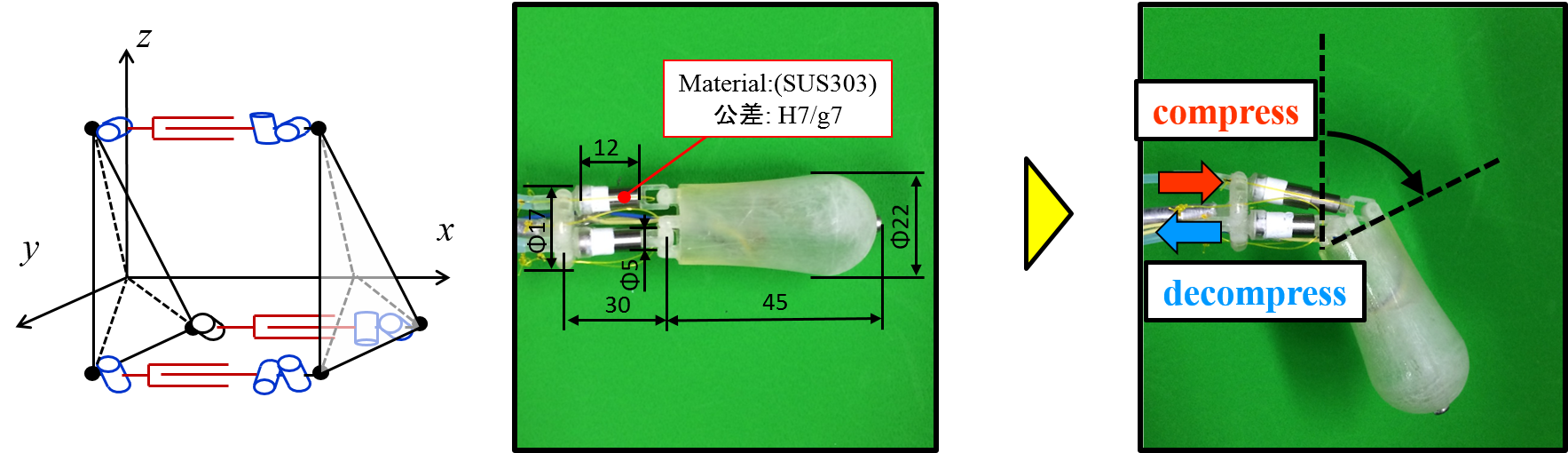
[Research paper (in
Japanese)]
野村幸暉,佐藤衛,竹内弘美,今野実,鳥海良一,石井裕之,高西淳夫,伸長ホースと径可変バルーンを用いた管内移動ロボットの開発,”第34回日本ロボット学会学術講演会”,
2U1-03,2016年9月
Speeding up pneumatic response
Overview
The deeper the robot went into the gas pipe, the more pronounced the air pressure response delay became due to the longer subsequent tubes, the greater the pipe resistance, and the greater the air volume required. The solenoid valve, which had been installed on the ground, was installed just before the robot because it would have taken a great deal of time to drive the robot and would have prevented efficient inspections. However, electricity cannot be used in gas pipes to avoid the risk of fire. Another problem with solenoid valves was their large size. Therefore, we designed a small valve that switches the flow path like a solenoid valve, and selected water pressure as the driving source, which can propagate energy responsively to deep areas far from the ground.
Hydraulic drive flow path switching unit
The hydraulic drive channel switching unit consists of two modules: the channel switching module and the on-off module. The flow path switching module allows the user to select which actuator to drive according to the sequential running pattern of WATER. Inside the unit is a channel body with engraved channels to each part of the robot, and the channel body is rotated by water pressure to switch the channels. The on/off module restricts the flow rate to prevent excessive expansion of the balloon used. This module also incorporates a channel body inside and opens and closes the flow path by applying water pressure.